about.
Jet Edge Ultra High Pressure Waterjet Systems
Brooks is excited to announce a new representation of Jet Edge Ultra High Pressure Waterjet Systems in New England! Since 1984, Jet Edge has been designing and manufacturing ultra-high-pressure waterjet technology that doesn’t back down. Jet Edge systems are especially suited for heavy-duty, high-volume applications where speed and accuracy combine to meet your production and customer goals.
ALL JET EDGE WATERJET SYSTEMS ARE PROUDLY MADE IN THE UNITED STATES OF AMERICA!
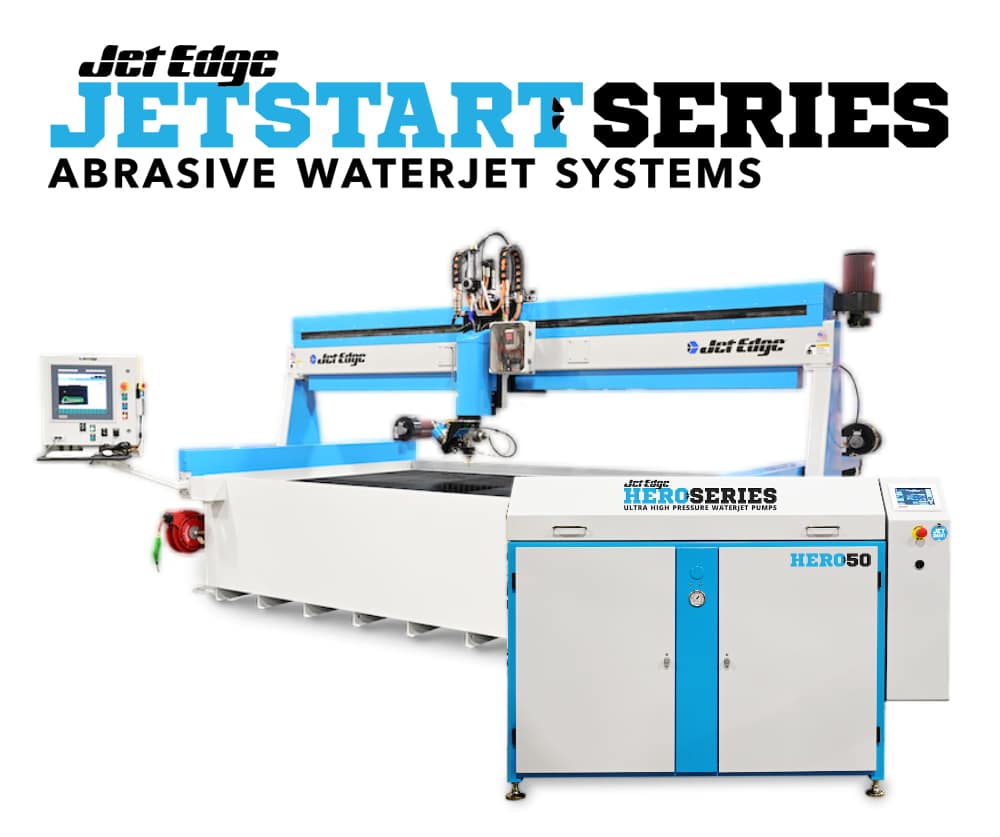
Jet Start Series
Jet Start Your Abrasive Waterjet Cutting
The Jet Start Series takes the no-nonsense workhorse 3-axis or 5-axis motion system and pairs it with Jet Edge’s HERO 50 intensifier pump that is loaded with features including Jet Smart controls.
HERO 50 & HERO 100 Intensifier Pumps
High Velocity Stream of Ultra High Pressure Water
The HERO 50 Waterjet Intensifier Pump, with Jet Smart Controls sets a new performance standard for UHP Intensifier pumps. Dependable and easy to maintain, the HERO 50 can cut and trim a large array of materials including heat sensitive metals, delicate foams, and tough substances like granite and glass.
Jet Edge allows you to custom configure your intensifier pump to match your unique application with the best value. If you require an engineering analysis to proof your processing goals, contact us today.
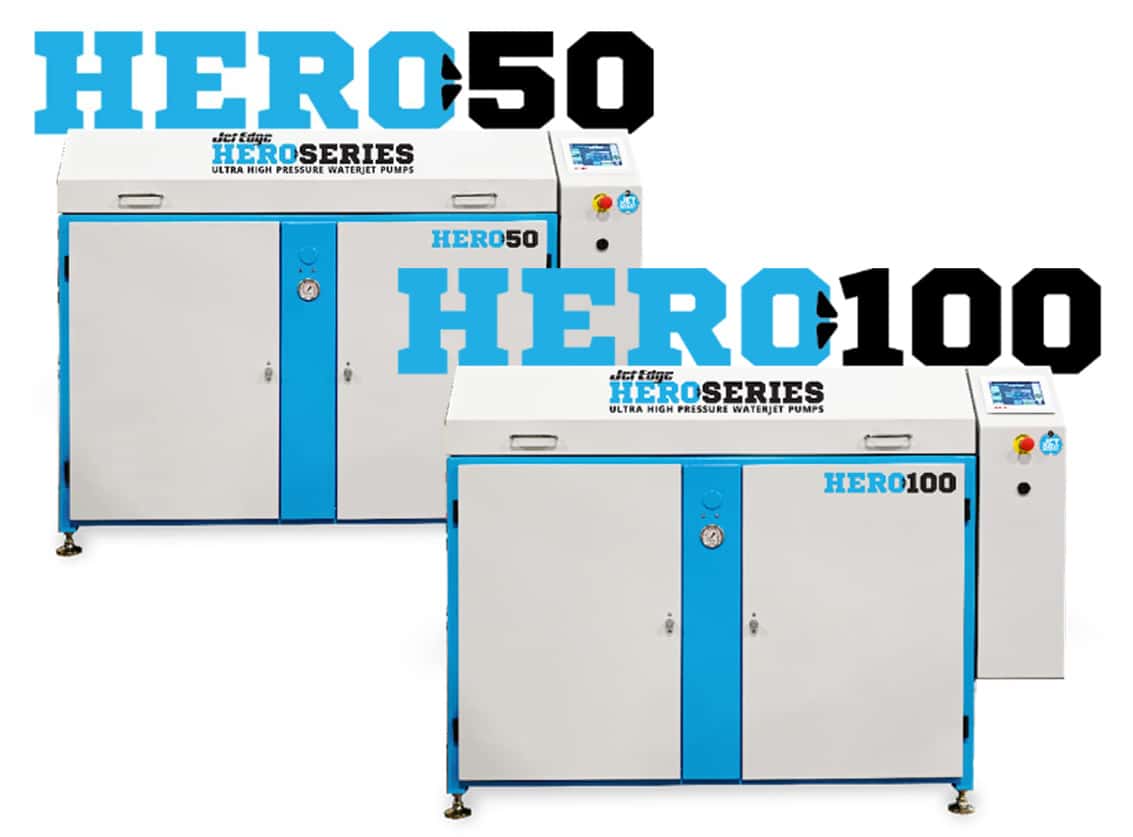
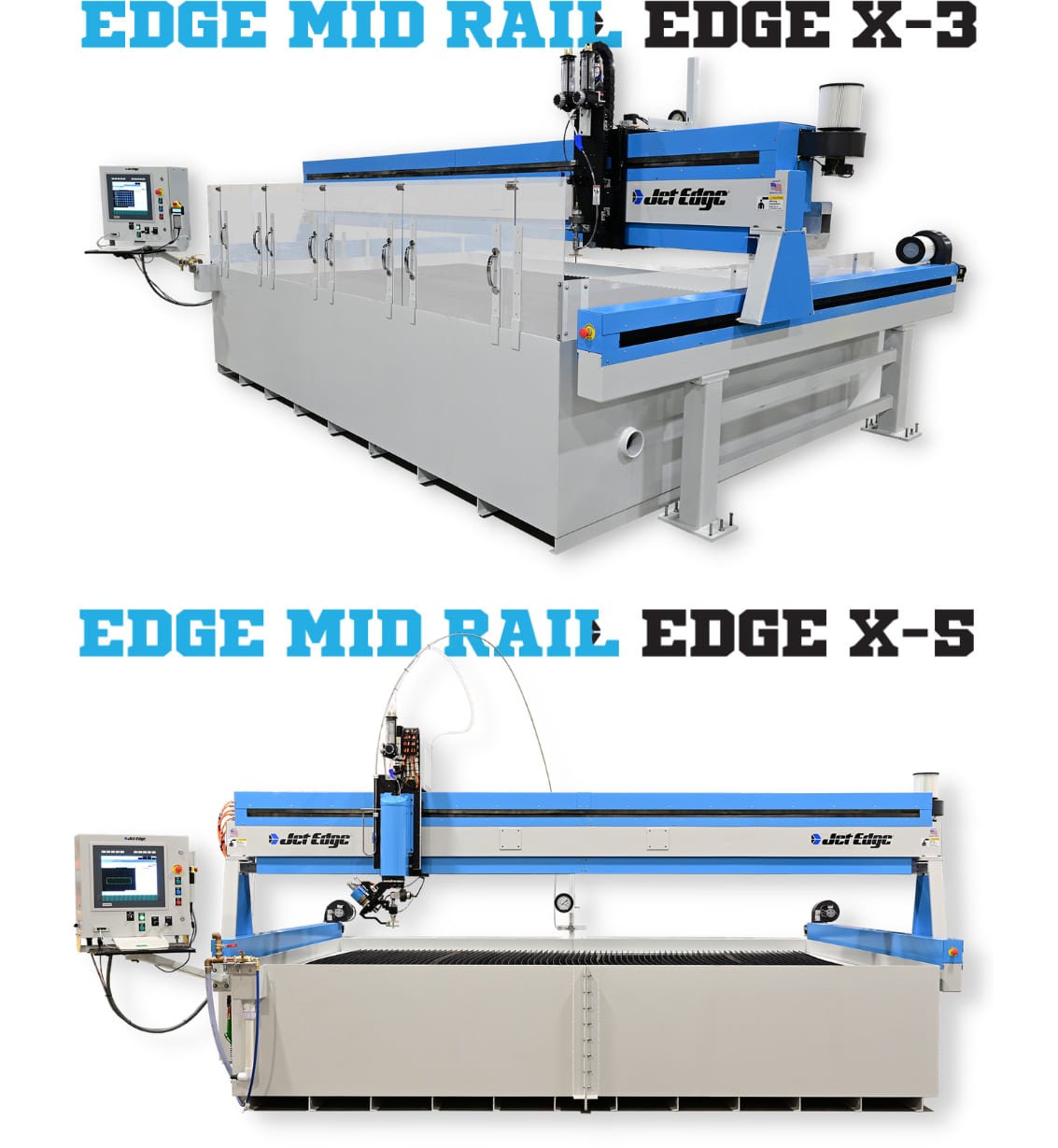
Edge Mid Rail Series
Edge X-3 & X-5 Mid Rail Waterjet Systems
The no-nonsense work horse in the waterjet industry. These brutes show up all day, every day to cut your toughest jobs with the highest precision and durability in the marketplace.
The Edge Mid Rail Systems have been in the marketplace since the technology went online, meeting the challenges of job shops, industrial manufacturing, aerospace, defense, stone, glass, foam, rubber, composites, textile, food and the list goes on. These systems are designed for heavy duty, high volume applications as well as delicate, fine detail waterjet cutting. Jet Edge is one of the few manufacturers, willing to custom engineer solutions to satisfy specific processing applications, making Jet Edge the go-to waterjet supplier for solving the world’s toughest waterjet problems. When paired with a Jet Edge, ultra-high pressure pump, the Edge Mid Rail motion systems can virtually cut anything…including costs!
benefits.
Customizable
We custom engineer solutions so you receive a system manufactured that satisfies your specific requirements. Our custom waterjet solutions have made us the go-to custom waterjet solution provider.
Have a unique application that water might help you solve?
High pressure water is used to clean, trim and cut across industries. Whether you are stripping paint from signs, degreasing aerospace engine components, slitting textiles or contour shape cutting, Jet Edge can help.
To learn more about Jet Edge’s custom application and custom configuration capabilities with ultra high pressure waterjets and if they are right for your operation, contact us today.
Precision Waterjet Cutter Motion Systems
Jet Edge industrial waterjet cutter motion systems lead the industry in precision and accuracy and are used by industrial fabrication and manufacturing facilities around the world, including machine and job shops, metal service centers, automotive, aerospace and defense manufacturers, stone and tile shops, and much more. Jet Edge also offers a line of entry-level low-cost waterjets that are ideal for budget-conscious shops.
Jet Edge systems are suited for heavy duty, high volume applications, to help customers solve their manufacturing challenges. Jet Edge is one of the few waterjet manufacturers willing to custom engineer solutions to satisfy specific cutting needs, making Jet Edge the go-to waterjet supplier for solving the world’s toughest waterjet problems. Jet Edge waterjets can cut virtually anything… including costs.
Post Installation Support
Jet Edge provides a standard warranty and an optional extended warranty on all of its equipment. The Jet Edge technical support line is manned 24 hours a day, 7 days a week, 365 days a year. Factory training at Jet Edge is provided free of charge during scheduled sessions. Scheduled Jet Edge maintenance programs can be taken advantage of to ensure your equipment is running at its peak, and programing training/support is also available.
solutions.
All About Waterjet Cutting in the Aerospace Industry
Every industry that requires precision-machined parts has its own set of unique manufacturing challenges. But it’s safe to say the aerospace industry is especially challenging and demanding. Parts in the industry can require:
- Extreme tight tolerances
- Extraordinarily complex shape geometries (5-axis vs 3-axis)
- Specialty materials with out-of-the-ordinary properties
- Small production runs
- Short-notice ordering
- Fines for discrepant or late deliveries
These characteristics create a very difficult manufacturing challenge which gets magnified when aircraft are involved, as component failures can result in the loss of life, payloads, aircraft or launch vehicles. In aerospace and defense, “close enough” results just aren’t “close to good enough.”
High-Volume Plate Cutting in the Metals Distribution Industry
Metals distribution companies play a pivotal role in the supply and manufacturing chain from raw ore to finished goods. With labor shortages and an increasing variety of specialty metals in demand, this role is becoming more important every day.
A high-level look at the metals industry material flow might look something like this:
- Ore extraction and refining
- Smelting, casting, coiling and rolling
- Intermediate shaping and preparation for distribution
- Creating stock materials – metals distribution companies
- Milling, machining and fabricating
- Finished goods
The products leaving the third stage frequently need further refinement into standard shapes, sizes and forms. These are the feedstock material the milling, machining and fabricating companies turn into finished goods.
Contract Manufacturing & Industrial Manufacturing
Jet Edge takes great pride in the range of industries our equipment supports. We are involved in steel distribution, industrial manufacturing, automotive and aerospace precision cutting, plastics, rubber, tool and die production, mining, food, and fabrics along with many more industries. Our willingness to custom-engineer solutions to satisfy specific needs makes us the go-to waterjet technology supplier.
contact us or request a demo.
To schedule a free application analysis or to request a demo, fill out the form below and one of our waterjet experts will reply as soon as possible.